Sintered NdFeB magnets are currently commercially available mass-produced permanent magnetic materials also known as neodymium magnets, is formed by neodymium, iron, boron, tetragonal crystal system crystals, is a high energy density of energy storage, can be highly efficient to achieve the energy and information of the mutual conversion of energy and its own energy is not consumed. Ultra-high energy density NdFeB permanent magnet materials to promote science and technology and information industry to integrated, thin, ultra-miniaturized, lightweight, intelligent development. Sintered NdFeB magnets are the most commonly used rare earth permanent magnet materials.
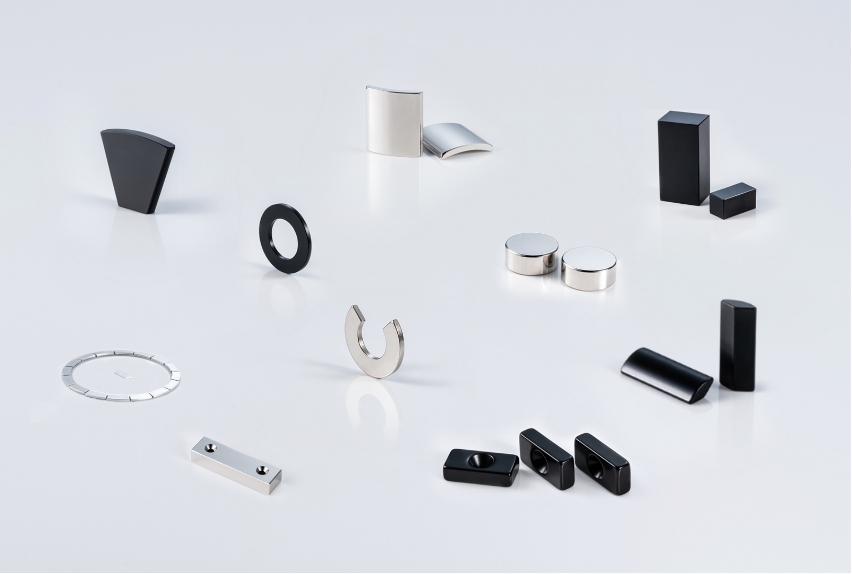
Thermal demagnetization state L/D=0.7 permanent magnet cylindrical samples (diameter D, orientation height L), saturated magnetization, in the open-circuit state, heated from room temperature to a constant temperature humidification 2h, and then cooled to room temperature, its open-circuit flux is not reversible flux loss ≤ 5% of the maximum humidification temperature.
Grade | (Br)KGs | (Hcb)KOe | (Hcj)KOe | (BH)maxMGOe | Hk/Hcj | (T)℃ |
N33 | 11.4~11.8 | ≥10.5 | ≥12 | 31~35 | ≥95 | 80℃ |
N35 | 11.8-12.3 | ≥11 | ≥12 | 33~37 | ≥95 | 80℃ |
N38 | 12.3~12.7 | ≥11.2 | ≥12 | 36~40 | ≥95 | 80℃ |
N40 | 12.7~12.9 | ≥11.4 | ≥12 | 38~42 | ≥95 | 80℃ |
N42 | 12.9~13.3 | ≥11.5 | ≥12 | 40~44 | ≥95 | 80℃ |
N45 | 13.3~13.7 | ≥11.6 | ≥12 | 43~47 | ≥95 | 80℃ |
N48 | 13.7~14.0 | ≥11.6 | ≥12 | 45~49 | ≥95 | 80℃ |
N50 | 13.9~14.2 | ≥11.4 | ≥12 | 48~52 | ≥95 | 80℃ |
N52 | 14.2~14.5 | ≥10.2 | ≥11 | 49~53 | ≥95 | 80℃ |
N54 | 14.4 14.8 | ≥10.2 | ≥11 | 50~54 | ≥95 | 80℃ |
35M | 11.8~12.3 | ≥10.9 | ≥14 | 33~36 | ≥95 | 100℃ |
38M | 12.3-12.6 | ≥11.5 | ≥14 | 36~40 | ≥95 | 100℃ |
40M | 12.6~12.9 | ≥11.8 | ≥14 | 38~42 | ≥95 | 100℃ |
42M | 12.9 13.3 | ≥12.0 | ≥14 | 40~44 | ≥95 | 100℃ |
45M | 13.3~13.7 | ≥12.5 | ≥14 | 43~46 | ≥95 | 100℃ |
48M | 13.6~14.0 | ≥12.9 | ≥14 | 45~49 | ≥95 | 100℃ |
50M | 13.9~14.2 | ≥13 | ≥ 14 | 47~51 | ≥95 | 100℃ |
52M | 14.2~14.6 | ≥12.5 | ≥13 | 49~53 | ≥95 | 100℃ |
35H | 11.8~12.3 | ≥11 | ≥17 | 33~37 | ≥95 | 120℃ |
38H | 12.3~12.6 | ≥11.4 | ≥17 | 36~40 | ≥95 | 120℃ |
40H | 12.6~12.9 | ≥11.7 | ≥17 | 38 ~42 | ≥95 | 120℃ |
42H | 12.9~13.3 | ≥12.0 | ≥17 | 40 ~44 | ≥95 | 120℃ |
45H | 13.3~13.7 | ≥12.5 | ≥17 | 43~47 | ≥95 | 120℃ |
48H | 13.7~13.9 | ≥12.8 | ≥16 | 45 ~49 | ≥95 | 120℃ |
50H | 13.9~14.2 | ≥12.9 | ≥16 | 47~51 | ≥95 | 120℃ |
52H | 14.2~14.5 | ≥12.8 | ≥16 | 48 ~53 | ≥95 | 120℃ |
33SH | 11.4~11.9 | ≥10.5 | ≥20 | 31~35 | ≥92 | 150℃ |
35SH | 11.8-12.3 | ≥11.2 | ≥20 | 33~37.5 | ≥92 | 150℃ |
38SH | 12.3~12.6 | ≥11.3 | ≥20 | 36.5~40 | ≥92 | 150℃ |
40SH | 12.6~12.9 | ≥11.8 | ≥20 | 38~41 | ≥92 | 150℃ |
42SH | 12.9~13.3 | ≥12.4 | ≥20 | 40~44 | ≥92 | 150℃ |
45SH | 13.3~13.7 | ≥12.5 | ≥20 | 43~46 | ≥92 | 150℃ |
48SH | 13.7~14.0 | ≥12.8 | ≥20 | 45~49 | ≥92 | 150℃ |
50SH | 13.9~14.2 | ≥12.9 | ≥20 | 47~51 | ≥92 | 150℃ |
52SH | 14.2~14.5 | ≥12.8 | ≥19 | 48~53 | ≥92 | 150℃ |
30UH | 10.8~11.4 | ≥9.5 | ≥25 | 28~32 | ≥90 | 180℃ |
33UH | 11.4~11.8 | ≥10.3 | ≥25 | 31~34 | ≥90 | 180℃ |
35UH | 11.8~12.3 | ≥10.6 | ≥25 | 33~37 | ≥90 | 180℃ |
38UH | 12.3~12.6 | ≥11.1 | ≥25 | 36~39 | ≥90 | 180℃ |
40UH | 12.6~12.9 | ≥11.5 | ≥25 | 38~41 | ≥90 | 180℃ |
42UH | 12.9~13.3 | ≥11.8 | ≥25 | 40~43 | ≥90 | 180℃ |
45UH | 13.3~13.7 | ≥12.2 | ≥24 | 43~46 | ≥90 | 180℃ |
48UH | 13.7~14.2 | ≥12.5 | ≥24 | 45~49 | ≥90 | 180℃ |
50UH | 13.9~14.3 | ≥12.8 | ≥24 | 47~51 | ≥90 | 180℃ |
52UH | 14.2~14.5 | ≥13.1 | ≥24 | 48~53 | ≥90 | 180℃ |
30EH | 11.0~11.4 | ≥9.5 | ≥30 | 28~31 | ≥90 | 200℃ |
33EH | 11.4~11.8 | ≥10.3 | ≥30 | 31~34 | ≥90 | 200℃ |
35EH | 11.8~12.2 | ≥11.1 | ≥30 | 33~36 | ≥90 | 200℃ |
38EH | 12.2~12.5 | ≥11.6 | ≥30 | 35~39 | ≥90 | 200℃ |
40EH | 12.5~12.8 | ≥11.9 | ≥30 | 37~41 | ≥90 | 200℃ |
42EH | 12.8~13.1 | ≥12.2 | ≥29 | 39~43 | ≥90 | 200℃ |
28TH | 10.5~10.8 | ≥9.5 | ≥35 | 26~29 | ≥90 | 230℃ |
30TH | 10.8~11.4 | ≥10.1 | ≥35 | 28~31 | ≥90 | 230℃ |
33TH | 11.4~11.8 | ≥10.2 | ≥35 | 31~34 | ≥90 | 230℃ |
35TH | 11.8~12.2 | ≥10.6 | ≥35 | 33~36 | ≥90 | 230℃ |
38TH | 12.2~12.5 | ≥11.6 | ≥33 | 35~39 | ≥90 | 230℃ |
Kind | Surface Colors | Physical property | Operating environment | Coating thickness |
Zinc plating | Blue and white, black, rainbow colors, etc. | Dense, stable and uniform surface | High corrosion resistance | 6um≤∮≤12 |
Electroplated nickel-copper-nickel | Silver White, Black | The plating has a metallic luster, uniform color and clean surface. | For use in more demanding environments | 15μm≤∮≤30pm |
Phosphide | Light gray | Uniform thickness | Slightly rustproof | |
Epoxy | Black, gray, some gloss | Uniform coating, insulation | For use in more demanding environments | ≥15μm |
Paraline Coating | Open (non-secretive) | Uniform thickness, dense, no pinholes, insulation | Suitable for extremely demanding environments | 0.1μm≤∮≤100pm |
Nickel + Copper + Epoxy | Black | Uniformity of coating, insulation, stability | Suitable for use in extremely harsh environments Salt spray >300hr | 10-30μm |
Aluminum + Epoxy | Black | Uniformity of coating, insulation, stability | Suitable for use in extremely harsh environments Salt spray resistant >650hr Suitable for new energy cycling automotive products | 15-35μm |
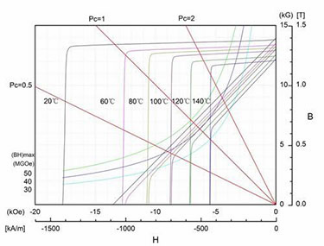
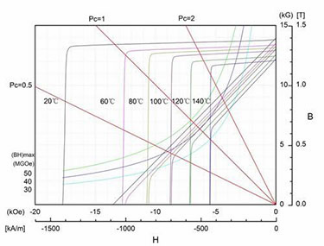
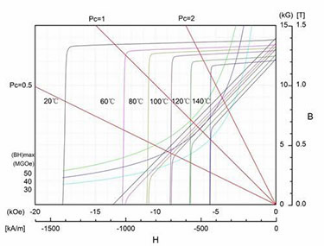
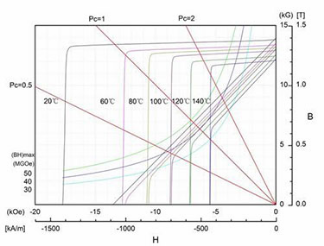
1, Size tolerance: length, width, thickness, diameter, etc. (tolerance range is generally not less than ± 0.05mm).
2, Shape and position tolerance: perpendicularity (≤ 0.8 °), parallelism (≤ 0.05mm), ellipticity (≤ 0.05mm), concentricity (≤ 0.05mm) and so on.
If the customer has requirements, the standard will be implemented according to the standard confirmed after negotiation with the customer.
Surface cleanliness (e.g., watermarks, color), degree of breakage (zinc loss, corner loss, knocked edges, black leather), cracks, sandholes, knife lines, etc.